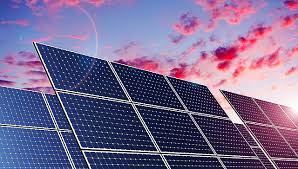
Application in new solar energy?
Silica gel has a variety of applications in the field of new solar energy, mainly involving solar cell manufacturing, solar module packaging, photovoltaic system installation and maintenance, etc.
Solar cell manufacturing:
Silica gel plays an important role in solar cell manufacturing. Silica gel can be used as an encapsulation material for solar cells to protect battery components from the external environment. Silicone’s high temperature tolerance and electrically insulating properties make it an ideal encapsulation material.
Solar module packaging:
Solar modules are usually made up of multiple solar cells, and silicone is used to encapsulate these cells and other key components. Silicone encapsulation can provide waterproof, dustproof and UV resistance to protect the performance of solar modules under different environmental conditions.
Inverter and electrical component packaging:
Inverters and other electrical components play a key role in solar systems, and silicone is also used for their encapsulation. This helps improve the weather resistance and stability of these devices, extending their service life.
Photovoltaic system sealing:
Silicone can be used for sealing and gluing in solar photovoltaic systems. It fills and seals the edges of solar modules, preventing moisture and dust from entering, improving system reliability and durability.
Solar water heater pipe connection:
In solar water heating systems, silicone can also be used to connect pipes and seal interfaces to ensure efficient operation of the system. Silicone’s performance stability under high temperature and humidity conditions makes it ideal for this purpose.
Solar photovoltaic cable protection:
Solar photovoltaic cables are exposed to different weather conditions in outdoor environments, and using silicone for protection can improve the weather resistance, waterproofing and insulation of the cables.
The application of silica gel in the field of new solar energy helps improve the performance, stability and lifespan of solar equipment, while protecting key components from the adverse effects of the external environment.
Application of silicone materials in lithium battery packs
Silicone materials have a variety of applications in lithium battery packs, mainly involving sealing, insulation, fixation and protection.
Sealing and Insulation:
Silicone materials can be used to seal the outer shell of lithium battery packs to prevent external moisture, dust or other harmful substances from entering the battery and affecting the performance and life of the battery. Silicone has excellent sealing performance and good insulation, ensuring that the battery can operate stably under various environmental conditions.
Fixed and buffered:
Within the battery pack, silicone can be used to secure and cushion battery components to prevent vibration and external shock from affecting the battery. This helps protect the internal structure of the battery and prevents parts from becoming loose or damaged.
Conductive plastic:
Sometimes, conductive materials may be added to silica gel to form conductive silica gel, which is used for connection, conduction and fixation inside the battery. This conductive property improves battery performance and stability.
Flame retardant coating:
In some demanding battery applications, silica gel can be used as a flame retardant coating to improve the fire resistance of the battery. This is important to ensure battery safety under extreme conditions.
temperature control:
Some silicone materials have excellent high temperature resistance and can be used for temperature control of lithium battery packs. In high-temperature environments, silicone can help stabilize the battery’s operating temperature and prevent overheating from causing safety issues.
Waterproof coating:
Lithium battery packs used outdoors or in harsh environments may require a waterproof coating to protect the interior of the battery from moisture. Silicone can provide effective waterproof properties, ensuring that the battery can still work properly in humid environments.
Silicone manufacturing
Silicone manufacturing involves the production of silicone, a versatile synthetic material with a variety of applications across industries. Silicones are polymers made of silicon, oxygen, carbon and hydrogen that offer unique properties such as flexibility, heat resistance, water resistance and biocompatibility.
Raw material preparation:
The main raw materials for silicone manufacturing are silicon (the key ingredient derived from quartz or sand) and methyl chloride. These raw materials undergo various chemical processes to produce monomers such as dimethyldichlorosilane.
Hydrolysis and polymerization:
The monomers undergo hydrolysis to produce silanol, which then polymerizes to form a silicone polymer. The polymerization process can be carried out by various methods, such as high temperature methods or using catalysts.
Modification and cross-linking:
Silicone polymers can be modified by adding various chemical groups to achieve specific properties. Cross-linking is a critical step that imparts stability and durability to the final silicone product. Cross-linking agents such as platinum are often used in this process.
Extrusion or molding:
After polymerization and modification, the silicone material is shaped into its final form through an extrusion or molding process. Extrusion involves forcing material through a mold to form a continuous shape, while molding involves shaping silicone within a mold.
Maintenance:
Curing is the process of applying heat to silicone materials to promote cross-linking and curing. This step ensures that the silicone reaches its desired physical and chemical properties.
QC:
Quality control measures are implemented throughout the entire manufacturing process. Various tests are performed to evaluate the consistency, strength, flexibility, and other key properties of silicones.
Molding manufacturing
According to the product requirements you need, through injection, molding and other methods, we can provide customized products, including appearance, logo, size, etc.
1. SILICONE Injection molding:
Step 1: Design and mold making
Product design: First, design the three-dimensional model of the product according to the customer’s needs, including appearance, size, logo, etc.
Mold Design: Next, make the injection mold required for the silicone product. The design of the mold needs to take into account the complexity and details of the product to ensure the quality and accuracy of the final product.
Step 2: Material preparation
Silicone Preparation: Select the appropriate type and color of silicone to ensure it meets the specific requirements of the product. Silicone is usually liquid and needs to be properly proportioned and mixed before injection molding.
Step 3: Injection Molding
Mold installation: Install the designed mold onto the injection molding machine.
Heating silicone: Heating silicone to a liquid state for injection molding.
Injection: Inject the heated silicone into the mold through an injection machine to ensure that the entire mold cavity is filled.
Curing: After the silicone cools and solidifies in the mold, the mold is opened to obtain the silicone product.
Step 4: Post-processing
Trimming and trimming: Trim the product to remove possible flash edges or remaining material to ensure a smooth appearance.
Inspection: Conduct quality inspection on the formed products to ensure that the size, appearance and quality meet customer requirements.
2. Molding:
Step 1: Design and mold making
As with injection molding, product design and mold design are carried out first.
Step 2: Material preparation
Silicone Preparation: Select the appropriate type and color of silicone to ensure it meets the specific requirements of the product. Silicone usually comes in sheets or blocks and needs to be cut according to the shape of the mold.
Step 3: Molding
Mold installation: Install the designed mold onto the molding machine.
Silicone placement: Place the cut silicone sheets or blocks into the mold.
Close the mold: Close the mold and apply appropriate temperature and pressure so that the silicone fills the entire mold and obtains the desired shape.
Curing: Maintain temperature and pressure for a certain period of time to solidify the silicone into a molded product.
Step 4: Post-processing
Remove the remaining material: Take the molded silicone product out of the mold and remove any remaining material or flash edges that may exist.
Inspection: Conduct quality inspection on the formed products to ensure that the size, appearance and quality meet customer requirements.
Grow-silicone
We are a professional silicone manufacturing company, we have 10 years of OEM customization experience, contact us to start customizing your silicone products and enhance your business