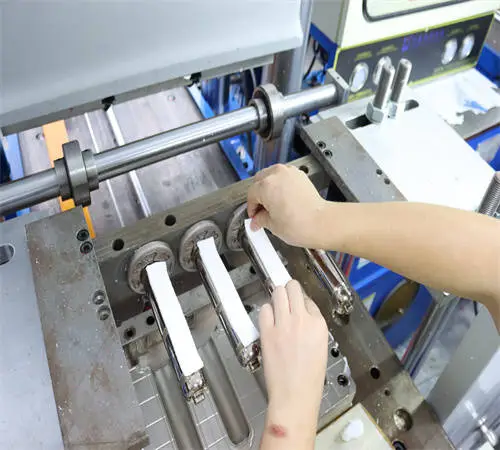
Common problems encountered in the production of custom silicone products We have been engaged in customized silicone products for 10+ years, and have served many well-known companies in Europe and America, such as Siliint , Muskie, we are in the industries of mother and baby, sports and pets. Accumulated very successful experience, but also encountered a lot of practical problems. Our business scope is mainly OEM customization. The regular customization solutions supported by silicone products include: logo, packaging, color, product shape, material.
The production process of silicone is also a complex , and bugs often appear. The most common problems include the following:
- Silicone products become brittle and damaged after a long time
- Insufficient elasticity
- The surface of transparent silicone products turns yellow
- The silk screen logo will fall off
- There are small honeycomb holes on the surface
- Color error
- There are impurities on the surface of the product,
- Silicone products have peculiar smell, etc.
As a top customized silicone products manufacturer in China, we have been working hard to improve:
- Establish a quality management system: formulate quality control processes, process specifications and related documents to ensure that each step meets quality requirements.
- Raw material selection and supply chain management: select reliable raw material suppliers and establish long-term cooperative relationships. Ensure that the quality of raw materials meets the requirements, and conduct inspections and verifications on a regular basis. Strictly control the incoming inspection of raw materials to avoid the use of low-quality raw materials.
- Process control: optimize the production process of silicone products to ensure that the operation of each step is carried out in accordance with the standard requirements. Strictly control temperature, humidity, time, and other process parameters to ensure product stability and consistency. Use suitable production equipment and tools to improve production efficiency and product quality.
- On-line detection and sampling inspection: Introduce on-line detection technology in the production process to monitor and control the quality of products in real time. At the same time, sampling inspections are carried out, and samples are regularly taken from the production line for laboratory testing to ensure that the quality of the products meets the standards.
- Training and employee participation: Provide comprehensive training to ensure that production operators understand quality requirements and operating procedures. Encourage employees to participate in quality control activities, such as exception reporting, improvement suggestions, etc., so that quality problems can be discovered and resolved in a timely manner.
- Process improvement and problem analysis: establish a culture of continuous improvement, conduct regular assessment and analysis of the production process, find potential problems and bottlenecks, and take measures for improvement. Use quality tools and methods, such as Statistical Process Control (SPC), Root Cause Analysis (RCA), etc., to resolve quality issues and prevent their recurrence.
- Customer feedback and market monitoring: Obtain customer feedback and market information in a timely manner to understand the actual application of products and customer satisfaction. Product improvement and optimization based on feedback to improve product quality and adaptability.
If you also encounter similar problems, welcome to discuss with us.
If you want to cooperate with us, you are also very welcome, you can enter the website to contact us.