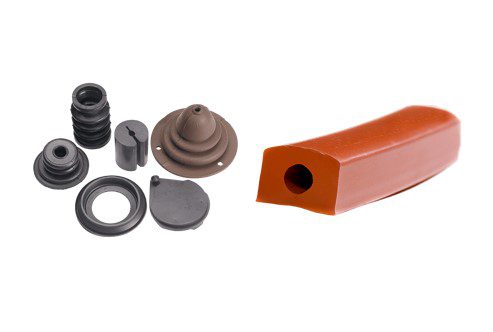
Table of Contents
Silicone Rubber is an elastic material with excellent performance and diverse applications. It is widely used in industry, medical, electronics, construction and other fields.
Silicone rubber is an elastic material made of silicone polymers such as Polydimethylsiloxane (PDMS). It has excellent properties such as high temperature resistance, low temperature resistance, electrical insulation, radiation resistance, and ozone resistance. These properties make silicone rubber an indispensable material in many fields.
Attention to environmental protection is gradually increasing, and research on environmental protection practices and sustainability in the manufacturing process of liquid silicone rubber has also become one of the development trends.
Liquid Silicone Rubber (LSR) is a special type of silicone rubber that has fluidity in a liquid state and is suitable for processing processes such as injection molding and compression molding.
Features and Applications:
High Temperature Stability: LSR has the high temperature resistance of silicone rubber and can typically operate in a temperature range of -50°C to 200°C.
Softness and elasticity: It has excellent softness and elasticity and is suitable for applications that require bending or stretching, such as flexible sealing rings, elastic parts, etc.
Chemical resistance: It has good chemical resistance and high stability to many chemical substances.
Electrical insulation: It has good electrical insulation properties and is suitable for packaging and insulation of electronic components.
Manufacturing process:
Injection Molding: LSR is often used in injection molding, where liquid silicone rubber is injected into a mold for molding. This method is suitable for producing large quantities of complex-shaped products.
Compression molding: Similar to compression molding of regular silicone rubber, but uses liquid silicone rubber in the process. After the mold is closed, the liquid silicone rubber solidifies in the mold to form the desired product.
development trend:
Innovative materials: New liquid silicone rubber materials are constantly being developed to improve their properties, such as wear resistance, aging resistance, etc.
Expansion of application fields: LSR is widely used in medical, food-grade appliances, baby products, auto parts and other fields, and more new fields may emerge in the future.
Intelligent manufacturing: Use digitalization and automation technology to improve production efficiency and reduce production costs.
1. Properties of silicone rubber
High temperature resistance: Maintains elasticity and stability in extreme high temperature environments. Low temperature resistance: It can still maintain flexibility at low temperatures and is not easy to become hard and brittle. Electrical insulation: Excellent electrical insulation properties, widely used in the electronic field. Ozone and radiation resistance: It has strong resistance to ozone and radiation. Biocompatibility: Suitable for medical devices and biomedical fields.2. Application of silicone rubber
Medical field: Used to manufacture medical devices, artificial organs, medical seals, etc. Electronics industry: As sealing materials, isolation pads, etc. for electronic components. Construction engineering: Used for sealing, insulation, earthquake resistance, etc. Automobile industry: Manufacturing sealing rings, rubber parts, sound insulation materials, etc.3. Future development trends
Silicone rubber may face the following trends in future development: Green environmental protection: In response to the demand for environmental protection and sustainable development, silicone rubber may develop in a more environmentally friendly and degradable direction. Innovative materials: According to the needs of different application scenarios, more innovative silicone rubber materials may emerge. Intelligent silicone rubber: Combined with intelligent technology, silicone rubber has functions such as sensing and response, expanding its application areas.The difference between Silicone Rubber and rubber
“Silicone Rubber” and “Rubber” are two different types of elastic materials with some significant differences:chemical components:
Silicone Rubber: It is a high molecular polymer composed of elements such as silicon, oxygen, carbon and hydrogen. It is usually made of silicone polymers such as polysiloxane (Polydimethylsiloxane, referred to as PDMS). Rubber: Usually refers to natural rubber, which is a polymer material processed from the latex secreted by rubber trees. Natural rubber is mainly composed of polyisoprene monomer.Temperature resistance and chemical stability:
Silicone Rubber: Has excellent high and low temperature resistance and is able to maintain its performance over a wide temperature range. At the same time, silicone rubber has good stability to many chemical substances. Rubber: Natural rubber has poor temperature resistance, is easy to harden at high temperatures, and is less stable to some chemicals.Elasticity and mechanical properties:
Silicone Rubber: Has excellent elasticity and flexibility, maintaining elasticity over a wide temperature range. Rubber: Natural rubber also has good elasticity, but is generally less adaptable to temperature than silicone rubber.use:
Silicone Rubber: Widely used in medical equipment, electronics, automobiles, construction and other fields, especially where high temperature resistance and electrical insulation properties are required. Rubber: Used in a wide range of applications including tires, seals, rubber mats, rubber tubing, etc. for general industrial and consumer applications.What is rubber made of?
Rubber is primarily made from the latex of the rubber tree (Hevea brasiliensis), a milky white liquid found primarily in the bark of the rubber tree. The following is the rubber preparation process: Rubber tree plant latex: The rubber tree releases rubber latex by cutting its bark. This latex mainly flows out from the latex tubes in the bark cells of the rubber tree and contains rubber particles, water, protein and other ingredients. Harvesting of rubber emulsion: The process of harvesting rubber is called rubber harvesting or rubber tapping. Rubber tappers make small incisions in the bark of the rubber tree to allow the rubber latex to flow into the container. Coagulation and drying: After the rubber emulsion is collected, it is transported to the rubber factory. In rubber factories, acids, sodium hydroxide and other substances are added to the emulsion, causing the rubber particles in the emulsion to solidify. The solidified glue block is chopped into pieces to form rubber blocks. Rubber processing: Rubber blocks are sent to rubber processing plants and undergo a series of processing steps, such as extrusion, drying, vulcanization, etc., to finally form rubber products. These products can include rubber bladders, rubber sheets, rubber tubes, rubber tires, etc. Vulcanization: Rubber undergoes vulcanization under the action of sulfur, a cross-linking reaction, to form rubber products with better physical properties. The vulcanization process increases the rubber’s elasticity, wear resistance and aging resistance. Final product: After processing and vulcanization, rubber products can be used in a variety of fields, including automotive tires, industrial seals, rubber tubes, rubber soles, etc.What is silicone made of?
Silicone is an elastic material made from silicone polymers. The following is the basic production process of silicone: Raw materials of silicone rubber: The main raw material is siloxane polymer, of which polysiloxane (Polydimethylsiloxane, PDMS for short) is the most common one. Silicone polymers are polymer compounds composed of elements such as silicon, oxygen, carbon and hydrogen. Pretreatment: Before preparing silica gel, the silicone polymer may need to undergo some pretreatment steps to ensure its purity and suitability. This may include steps such as removing impurities and adjusting molecular chain length. Cross-linking agent: In order to make silicone elastic and soft, a cross-linking agent needs to be added. These cross-linking agents form a cross-linked structure between siloxane polymer molecules and enhance the three-dimensional network structure of the silica gel. Adding Pigments and Additives: Pigments and other additives can be added to silica gel to change its color, hardness, viscosity and other properties to make it more suitable for specific uses. Stirring and mixing: Raw materials, cross-linking agents and other additives are mixed evenly through mechanical stirring to ensure that they are fully integrated. Heating and curing: The mixed silicone raw materials usually need to be heated to harden and solidify at a certain temperature and time. This step is called curing or cross-linking of the silicone. Forming and cutting: The cured silicone block can be made into silicone products of the required shape and size through forming and cutting processes, such as silicone pads, silicone sealing rings, silicone tubes, etc. The preparation process of silica gel is relatively flexible and can be adjusted according to specific requirements and uses. The characteristics of this material include excellent high temperature resistance, soft elasticity, electrical insulation, etc., so it has been widely used in medical, electronics, cooking tools, seals and other fields. As two important raw materials widely used in industry, silicone rubber and rubber play an indispensable role in all areas of life. Their unique properties make our lives more convenient and comfortable. Silicone rubber has become an ideal choice for medical, electronic and other fields due to its high temperature resistance and electrical insulation properties, while traditional rubber plays an important role in automobile tires, seals, etc. One thing these two have in common is that they both have excellent elasticity and wear resistance, making them widely used in many fields such as manufacturing, construction, medical, and home furnishings. In different application scenarios, they show unique characteristics and advantages, providing solid support for technological innovation and production efficiency in various industries. It is precisely because of the excellent properties of silicone rubber and rubber that we can enjoy a safer, more comfortable and more efficient life in modern society. With the continuous development of science and technology, these two are also constantly evolving and innovating, laying a solid foundation for our future life. Whether it is silicone rubber for medical technology or rubber products that support transportation, they are indispensable materials in the industrial field and play an important role in creating a better future for us.grow-silicone:
We are a silicone rubber product manufacturer from China, Excellence in design and innovation: We lead the design and innovation of silicone rubber products. The team has experienced designers and engineers dedicated to providing customers with unique and practical solutions. We not only meet your needs, we shape the future with innovation. Advanced production capabilities: With first-class production equipment and technology, we provide you with excellent quality silicone rubber products with efficient and precise production processes. Whether it’s complex custom design or mass production, we have exceptional execution capabilities. Strict quality control: Quality is our strongest commitment. From raw material procurement to production and manufacturing, we strictly follow the ISO quality management system to ensure that every product meets the highest standards. Extremely Competitive Price: We understand that in a highly competitive market, price is one of the key factors in determining purchasing decisions. Therefore, we provide you with highly competitively priced silicone rubber products based on high efficiency and lean production. Global service network: No matter where you are, we can provide responsive global services. Our service network covers the world, ensuring that you can obtain the products and support you need in a timely and convenient manner.Liquid silicone rubber
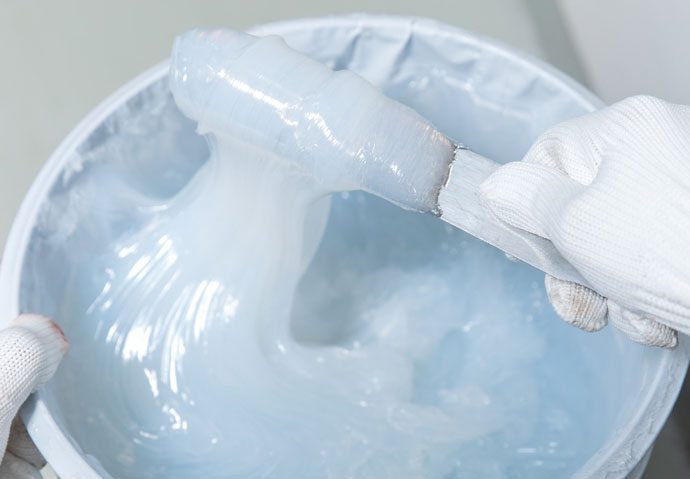