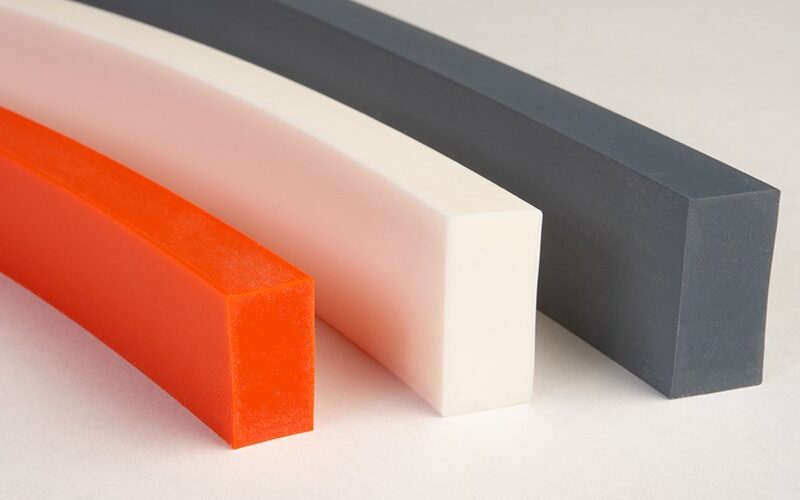
Is the higher the hardness of silicone, the better? NO!
Measurement standard for silicone material hardness:
Silicone hardness is usually expressed by Shore hardness, the most common being Type A and Type D hardness. Shore hardness is expressed by applying a certain amount of pressure to the surface of the material using a hardness tester and then measuring the depth of the indentation.
Shore A Hardness: Suitable for soft materials such as rubber and elastic materials. The tip of the durometer is pushed into the material surface using a specific spring load and the depth of the indentation is read. Silicone hardness is generally in the Shore A range, with higher values indicating harder silicone.
Shore D Hardness: For harder materials such as plastics and ebonite. The test method is similar to Shore A, but the parameters of the durometer and spring used are different. The higher the Shore D hardness number, the harder the silicone is.
The choice of silicone hardness often depends on the needs of the specific application:
Softer hardness (lower Shore A value):
Suitable for applications that require higher elasticity and flexibility, such as some silicone seals or hoses that require better sealing.
Medium hardness (medium Shore A value):
Suitable for general silicone products, such as silicone baby pacifiers, handles, etc.
Harder hardness (higher Shore A number or Shore D number):
Ideal for applications requiring greater stiffness and wear resistance, such as silicone gaskets, silicone overlays for electronic components, etc.
When choosing silicone hardness, consider the material’s properties such as elasticity, tensile strength, abrasion resistance, and desired softness. The choice of hardness is critical to ensuring that silicone products perform well under specific environmental and use conditions.
What are the applications of different hardnesses in silicone manufacturing?
The selection of different silicone hardnesses has wide application in silicone manufacturing, because the hardness of silicone directly affects its mechanical properties, elasticity and application range. Here are some common manufacturing applications of silicones of varying hardness:
Softer hardness (Shore A 10-30):
Application: Suitable for applications requiring a high degree of softness and elasticity.
Examples: Baby pacifiers, straws, soft seals, etc.
Medium hardness (Shore A 40-60):
Application: Universal performance, can meet a variety of requirements, ranging from soft to hard.
Examples: Medical device seals, industrial gaskets, handles, sealing rings, etc.
Harder hardness (Shore A 70-90):
Application: Suitable for applications requiring higher hardness, rigidity and wear resistance.
Examples: Outsourcing of electronic components, automotive parts, gaskets, etc.
Extreme hardness (Shore D):
Application: Suitable for special requirements and occasions requiring high hardness and wear resistance.
Examples: High temperature resistant seals, industrial sealing components, mechanical parts, etc.
The choice of silicone hardness depends on the needs of the specific application:
Seals and Gaskets: Softer hardness silicones are often used to provide good sealing, such as door and window seals, pipe gaskets, etc.
Medical devices: Medium-hard silicone is often used to make seals for medical devices, such as various envelopes and sealing rings.
Auto parts: Harder silicones can be used in auto parts, such as hood seals and suspension components.
Electronic component packaging:Harder silicone is used to provide protective packaging for electronic components to ensure durability under harsh conditions.
In practical applications, the choice of silicone hardness is determined based on specific engineering requirements, environmental conditions, and material characteristics. Different hardnesses of silicone provide flexibility, making it an excellent material for a wide range of applications.
What are the advantages and disadvantages of high hardness?
Silicone with high hardness usually has some advantages and disadvantages, and these characteristics will have different effects in different application scenarios. Here are some common pros and cons of hard silicone:
advantage:
Wear resistance and durability: Silicones with higher hardness are generally more resistant to wear and durability, so they perform well in applications where they need to withstand friction and pressure.
Ability to maintain shape: Silicone with high hardness is more likely to maintain its original shape and structure and is less prone to deformation, so it is advantageous in applications where precise dimensions need to be maintained.
High temperature resistance: Some silicone materials with high hardness can still maintain their physical properties under high temperature conditions and are suitable for applications in high temperature environments.
Better tensile strength: Higher hardness is usually accompanied by better tensile strength, making it perform well in applications that can withstand tensile forces.
Better chemical stability: Some high-hardness silica gels are more resistant to chemicals and have better chemical stability.
shortcoming:
Less flexible: High-hardness silicones are relatively rigid and may lack flexibility, making them unsuitable for certain applications that require a high degree of bending and stretching.
Poor impact absorption: In applications that require better impact absorption, silicone with higher hardness may perform poorly and be prone to breakage or breakage.
Poorer sealing: Due to its high hardness, silicone may be less elastic and may not perform as well as softer silicones in some sealing applications.
Manufacturing and Processing Difficulty: Due to its high hardness, processing and manufacturing of silicone can be more challenging and may require more advanced processes and equipment.
Higher cost: Generally speaking, silicone materials with higher hardness are more expensive to manufacture, which may be a consideration in some cost-sensitive applications.
Overall, harder silicones are suitable for applications where rigidity, abrasion resistance and durability are important, but may not be suitable where flexibility and impact absorption are required.
What are the advantages and disadvantages of low hardness?
Silicones with low hardness usually have some advantages and disadvantages, and these characteristics will have different effects in different application scenarios. Here are some common pros and cons of low-hardness silicone:
advantage:
Better Flexibility: Lower durometer silicones are generally softer and more elastic, making them suitable for applications that require bending, stretching, and twisting.
Better impact absorption: Where better impact absorption is required, silicone with lower hardness performs better and helps reduce impact.
Better sealing: Due to its low hardness, silicone is easier to deform and adapt to irregular surfaces, so it performs well in some sealing applications.
Easy to process and manufacture: Due to its softness and low hardness, silicone is relatively easy to process and manufacture, and is suitable for some special shapes or details.
Lower cost: Generally speaking, silicones with lower hardness are less expensive to manufacture, which may be more attractive in some cost-sensitive applications.
shortcoming:
Relatively Poor Wear Resistance and Durability: Due to their softness, silicones with low hardness may have poor wear resistance and durability and are not suitable for highly abrasive applications.
Poor tensile strength: Relatively soft silicones may perform poorly in applications that withstand tensile forces.
Not suitable for high-temperature environments: Some silicones with lower hardness may degrade in high-temperature environments and are not suitable for high-temperature applications.
May be more difficult to maintain shape: Due to their softness, low-hardness silicones may perform poorly in some applications where shape retention is required.
Generally speaking, low-hardness silicone is suitable for applications that require flexibility, deformability, and sealing, but may not be suitable in some situations where higher strength and durability are required. Choosing the most appropriate silicone hardness should balance these advantages and disadvantages based on the needs of the specific application.
How is the hardness of silicone made?
The hardness of silicone rubber is achieved by adjusting the type and amount of hardener during the preparation process of silicone rubber. Silicone rubber is a polymer material composed of silicon-oxygen chains, and its hardness can be controlled by adjusting the degree of cross-linking and the type of hardener. The preparation of silicone rubber usually includes the following key steps:
Silicone base material selection: Choose a suitable silicone base material, which is usually liquid silicone rubber. Silicone base materials include siloxane and silane.
Selection of hardener: Select the hardener. The type and proportion of the hardener will directly affect the hardness of the silicone. Hardeners can be organic tin compounds, peroxides, etc.
Mixing: Mix the silicone base material and hardener thoroughly. The mixing process may include steps such as stirring, stirring vacuum, and standing to ensure the uniformity of the silicone rubber.
Shaping: Place the mixed silicone rubber into the mold or shape required for the application. Molding can be coating, injection, casting and other different processes.
Curing: Place the molded silicone rubber under appropriate conditions for curing. The curing of silicone rubber is usually accomplished by baking, natural curing or heat curing.
Growsilicone silicone manufacture:
As a professional custom manufacturer of silicone products, we will first evaluate the silicone products you want to customize based on many years of industry experience, and provide professional suggestions on what hardness materials are needed. If you still cannot determine the application of your customized products, we can When developing silicone prototypes, samples of different hardnesses are made for you to choose from. In the end, the silicone manufacturer can adjust it according to customer needs and product uses!
Contact us to get a professional and fast quote and professional answers!